Manual Handling in the Workplace
What is Manual Handling?
Manual handling refers to the movement or support of objects by human force. This includes lifting, carrying, pushing, and pulling activities. Improper manual handling can lead to various health issues, particularly musculoskeletal problems, causing long-term pain and potential disability.
Why is Manual Handling at Work Important?
Understanding and adhering to proper techniques in manual handling at work is crucial. A significant percentage of work-related injuries are attributed to poor manual handling techniques, resulting in numerous lost work hours. By fostering awareness and proper practice, we can:
- Reduce injuries among workers.
- Decrease work-related health complications.
- Increase productivity by preventing lost work hours.
- Promote a safer, healthier working environment for all.
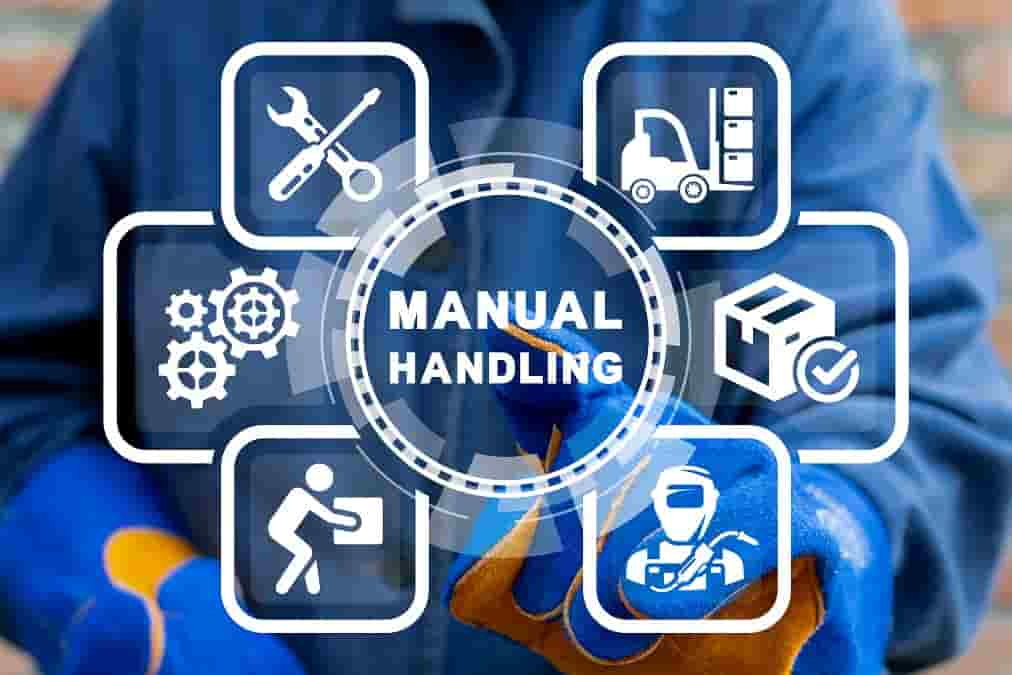
Manual Handling Training: A Necessity
To combat the risks associated with manual handling and reduce lost work hours, it’s imperative that workers receive adequate manual handling training. This training focuses on:
- Identifying Risks: Recognizing potential hazards related to lifting, carrying, and moving objects.
- Proper Techniques: Understanding the right way to perform manual handling tasks. This includes the correct posture, the mechanics of lifting, and the use of assistance when needed.
- Use of Equipment: Introducing tools and devices that can help in manual handling tasks, such as trolleys or mechanical aids.
- Maintaining Health: Offering advice on physical fitness and exercises that can help in strengthening the body for manual tasks.
Invest in Training, Reap the Benefits
The Workers Union strongly believes that investing in manual handling training can significantly decrease the number of injuries, ensuring that workers remain safe and healthy. Furthermore, by reducing the incidents of injury, we can also lessen the number of lost work hours, promoting productivity and well-being.
For organizations, the benefits are two-fold:
- Cost Saving: Fewer injuries mean less expenditure on medical treatments, compensations, and lost productivity.
- Reputation Building: A safer workplace leads to happier employees and builds the company’s image as a caring, responsible employer.
In Conclusion
Manual handling is an integral aspect of many jobs. With the right training and awareness, we can ensure that these tasks are performed safely, minimizing risks and maximizing efficiency.
The Workers Union stands by its commitment to promote the health and safety of every worker. Invest in manual handling training today, and pave the way for a safer, more efficient workplace tomorrow.
Frequently Asked Questions
In the UK, the primary regulation for manual handling is the Manual Handling Operations Regulations 1992 (MHOR). These regulations set the guidelines for employers to ensure the health and safety of their workers engaged in manual handling tasks.
A manual handling risk assessment is an evaluation of the potential risks involved in manual handling tasks in a particular workplace. Employers are required by law (under MHOR) to carry out these assessments to identify high-risk manual handling tasks and implement controls to minimize the risks.
Manual handling training typically covers proper lifting techniques, risk assessment, and ways to minimize strain and injury. Training can be provided in-house by qualified staff or through external courses that are compliant with national guidelines.
Employees have the right to refuse to perform tasks that they believe pose an immediate and serious danger to their health and safety. However, this is generally a last resort, and issues related to manual handling should ideally be resolved through risk assessments, training, and proper equipment.
There are no specific weight limits set by the Manual Handling Operations Regulations. However, employers are obligated to conduct a risk assessment and take appropriate steps to reduce the risk of injury from manual handling tasks. This may include setting weight limits based on the assessment and the capabilities of the workforce.